

Crane Configuration: Items to Consider
When specifying a crane configuration, some obvious items come to mind: crane make and model, boom length, and amount of counterweight. But what other items must be considered when configuring a crane?
December 2020 | Updated January 2025
A complete crane configuration is essential for any pick plan to ensure that the crane functions as intended when performing a lift. When discussing crane configuration, some items may initially come to mind: make, model, boom length, and counterweight. While these are primary aspects of a crane’s configuration, there are additional items that must be checked and specified prior to performing a pick. Although specific makes and models may require some additional considerations, this article focuses on the following:
-
Number of line parts
-
Length of wire rope required
-
Number of sheaves required
-
Minimum overhaul weight
-
Block selection
Each item must be checked for each hoist on the crane. Therefore, if a crane utilizes an auxiliary hoist (whip), separate checks must be performed for the whip and the main.
Number of Line Parts
After selecting the crane make, model, and length of boom, the number of line parts can be determined. The hoist line must be capable of lifting all suspended weight below: including the lifted piece, rigging, and hook block. When the hoist line is not capable of picking the load, additional parts of line must be added. Each additional part reduces the load in the line and increases the total capacity of the hoist. Auxiliary hoists typically only use one or two parts of line, but the main hoist can have several parts of line depending on the crane size and the load picked. [1]
The operator’s manual will have a table that lists the total line capacity for different line parts. However, when planning a lift, that information may not be readily available, especially if the crane has not been procured. Although the operator’s manual must be consulted prior to performing the actual lift, there is a way to approximate total line capacity and determine the parts of line required. [2]
While crane product manuals typically do not provide capacities for each reeving, they do provide a maximum allowable line pull: the capacity for a single part of line. Dividing the suspended weight by the maximum allowable line pull provides a rough approximation of the line parts required but does not account for losses due to friction at each sheave. For few line parts, the losses are small, but for several parts of line, friction must be considered as it significantly affects the total capacity of the hoist.
The Crosby® General Catalog [3] provides a useful table that accounts for losses due to friction when considering number of line parts. That information is summarized in Table 1 which provides the capacity for different parts of line relative to the maximum line pull. As indicated by the table, the efficiency reduces as the number of line parts increases. For instance, ten parts of line are only capable of lifting 8.98 times the maximum line pull. To determine the required parts of line, divide the suspended weight by the maximum line pull and compare the result to the table to find the next highest line pull multiplier value. The corresponding parts of line would then be the minimum required line parts.
Table 1 – Line Pull Multiplier for Parts of Line
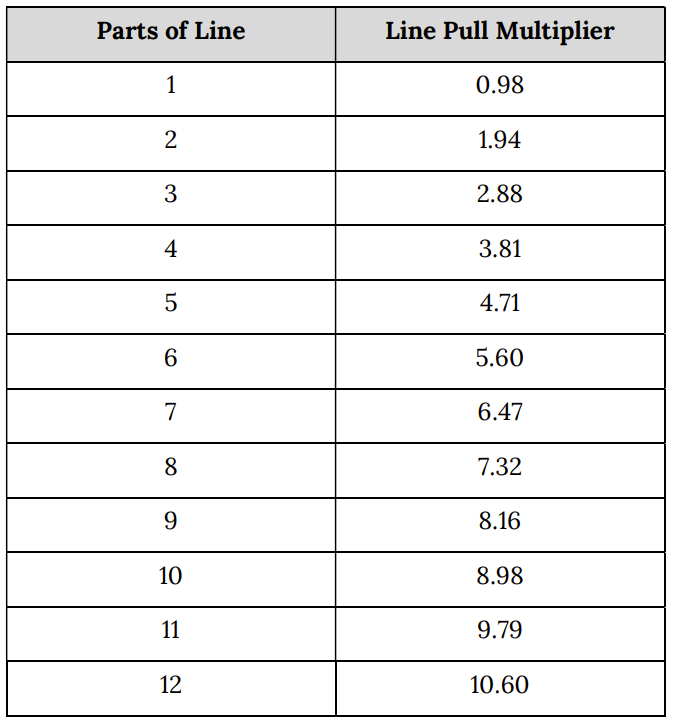
Example:
Piece weight: 80,000 lbs
Rigging: 8,000 lbs
Block weight: 5,500 lbs
Max allowable line pull: 27,500 lbs
First, calculate that the total suspended load is 93,500 lbs. Next, divide the total suspended load by the line pull to obtain a value of 3.40. Using the table, the smallest line pull multiplier value that is greater than 3.40 is 3.81 and corresponds to four parts of line. Therefore, four parts of line are required.
Length of Wire Rope Required
After determining the parts of line, the length of wire rope required can be calculated. The length of wire rope on the main hoist (or aux. hoist) is not standard and the vendor has to provide enough wire rope to ensure that the crane can operate as intended.
The total wire rope required is the summation of the length required below the boom tip, the length required on the back side of the boom, and the minimum length required on the drum. The length of wire rope along the backside of the boom can be approximated to equal the boom length and the minimum length on the drum can be taken as 200 ft to ensure a couple wraps are always on the drum. Putting these items into an equation generates:
Length Req’d = Parts of Line x (Boom Tip Elev. – Hook Elev.) + Boom Length + 200ft
When picks are required below the elevation of the crane, the additional depth is considered as shown in Figure 1. When working at or above the crane’s elevation, the distance between the boom tip and the hook can be approximated as the boom length, and the equation above can reduce to:
Length Req’d = (Parts of Line + 1) x Boom Length + 200ft

Figure 1: Crane Elevation
Sometimes a crane is reconfigured onsite and the parts of line or boom length change. When there is not enough wire rope to accommodate the required parts of line, the entire hoist line must be swapped with a new, longer spool. Identifying the need for more wire rope up front saves on the purchase of the additional spool and the labor required to swap out the hoist line. [4]
Number of Sheaves Required
The minimum number of sheaves required is determined based on the number of line parts using the following formula and rounding your answer to the nearest whole number.
Min No. of Sheaves = 1/2 x (Parts of Line - 1)
For instance, using the formula provides a result of 2.5 for 6 parts of line. Thus, 6 parts of line requires 3 sheaves. Table 2 provides the number of sheaves required for different parts of line. Blocks typically have odd numbered sheave increments: 1-sheave, 3-sheave, 5- sheave, and so on.
Table 2 – Sheaves Required for Parts of Line

Minimum Overhaul Weight
The minimum overhaul weight refers to the minimum suspended weight that will prevent the hoist line from becoming slack on the hoist drum. The overhaul weight must be heavy enough to offset the weight of the single part of line running down the back side of the boom. Insufficient overhaul weight may result in the inability to lower the hoist, or worse, cause the hoist line to overhaul the load block causing a two-block. [5] Typically, only the Crane configuration: Items to consider 4 block weight is considered as overhaul weight because it usually is the only item that always remains on the hoist line. The parts of line below the boom tip should not be considered as overhaul weight because their weight varies with the height of the block. When the block is lifted to its maximum height, the weight of the line parts below the boom tip is negligible.
As the boom length increases, the length of hoist line on the back side of the boom increases and the required overhaul weight increases. Furthermore, as the number of line parts increases, the load in the line decreases and the required overhaul weight increases. Thus, changes to parts of line or boom length affect the required overhaul weight.
The operator’s manual will have a table that specifies the minimum overhaul weight based on boom length and parts of line. However, like determining the total capacity of the hoist line, this information may not be readily available during planning. Still, we can approximate the minimum required overhaul weight by using a formula and table provided in the Crosby® General Catalog. [3] [6]
Min Overhaul Weight = (Boom Length x Wire Rope Unit Weight + Drum Friction) x Overhaul Factor
Crosby® provides the unit weight for 6x19 wire rope in their catalog. However, most crane hoists are not 6x19 wire rope and the weights provided for 6x19 wire rope are typically less than the actual weight of the hoist cable. Thus, we recommend using the values provided in Table 3. If the drum friction is unknown, Crosby® recommends using a value of 50 lbs. The overhaul factor accounts for the parts of line and is listed in Table 4. [3]
Table 3 – Wire Rope Weight
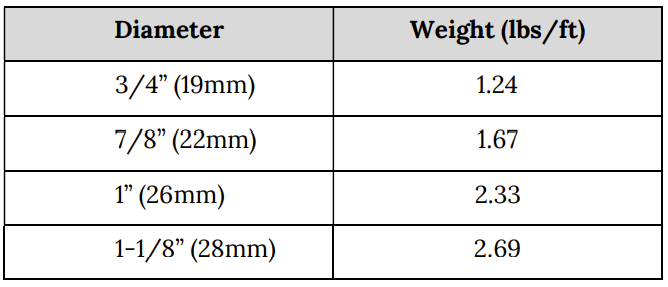
Table 4 – Overhaul Factors

Example:
Parts of Line: 6
Wire Rope Size: 26 mm
Boom Length: 180 ft
Drum Friction: Unknown
Since the drum friction is unknown, we can assume a value of 50 lbs. From Table 3 we determine that 26mm wire rope weighs 2.33 lbs/ft and from Table 4 we find that the overhaul factor for 6 parts of line is 6.54. Plugging these values, along with the boom length, into the equation, we obtain:
(180 ft x 2.33 lbs/ft + 50 lbs) x 6.54 = 3,070 lbs
Thus, 3,070 lbs of overhaul weight are required and the block must weigh more than 3,070 lbs.
Important Note on Boom Backwards Stability:
There may be special requirements, particularly with crawler cranes, when making picks at high boom angles. For some crane models, the load chart indicates that certain pick radii are only achievable based on having a minimum load on the hook. The minimum required load could be significantly greater than the required overhaul weight calculated above. Always be aware of stipulations outlined on the load chart or in the operator’s manual.
Block Selection
There are three considerations for selecting a block: block capacity, number of sheaves, and block weight. First, the block capacity must be capable of lifting all weight below the hook: the piece weight and all rigging. Next, the block must have enough sheaves to accommodate the required parts of line. Lastly, the block must weigh more than the minimum overhaul weight.
Larger blocks containing several sheaves can accommodate several parts of line and thus require additional overhaul weight. To provide the additional weight, larger blocks typically offer the option to add cheek weights: additional weight that can be attached to the block. Cheek weights are solely used to provide additional overhaul weight and are added in pairs. Refer to the crane’s product manual for information on the cheek weights available for the various block sizes associated with the crane. When selecting a block, also specify how many cheek weights are required. If none are required, leaving the cheek weights off the block could save a couple thousand pounds of deducts for your pick.
Jordan Roberts is the President of J.A.Roberts Co.
Special thanks to Mike Valjas of JF Lomma Inc. for contributing to this article.
-
As the number of line parts increases, the speed at which the hoist lifts the load decreases. Although some operations require the use of two hooks simultaneously, most cranes utilize a whip line to save time when picking lighter loads. For instance, a main block with 8 parts of line will take 8x longer to pick a load compared to a single part whip line. Thus, the reason for limiting the whip to one or two parts of line.
-
Table 1 is intended as a guide only. All total line capacity information must be confirmed with the operator’s manual associated with the crane’s serial number.
-
Crosby General Catalog. The Crosby Group LLC, 2019.
-
When procuring a crane, the vendor will typically calculate the length or rope required based on the initial boom length and parts of line specified. However, they may not ask to clarify 1) whether picks are made below grade or 2) whether you plan to have a future configuration that requires additional wire rope.
-
When the load block overhauls, the weight of the hoist line on the back side of the boom free falls thus lifting the block in an uncontrollable manner. The load block will continue to run upwards until it contacts another object, usually the boom tip. This contact is called a two-block and can cause significant damage. Avoidance of overhauling and two-blocking are critical considerations when planning a lift.
-
The overhaul formula and Tables 3 and 4 are intended as guides only. All information pertaining to minimum overhaul weight and wire rope weight must be confirmed with the operator’s manual associated with the crane’s serial number.